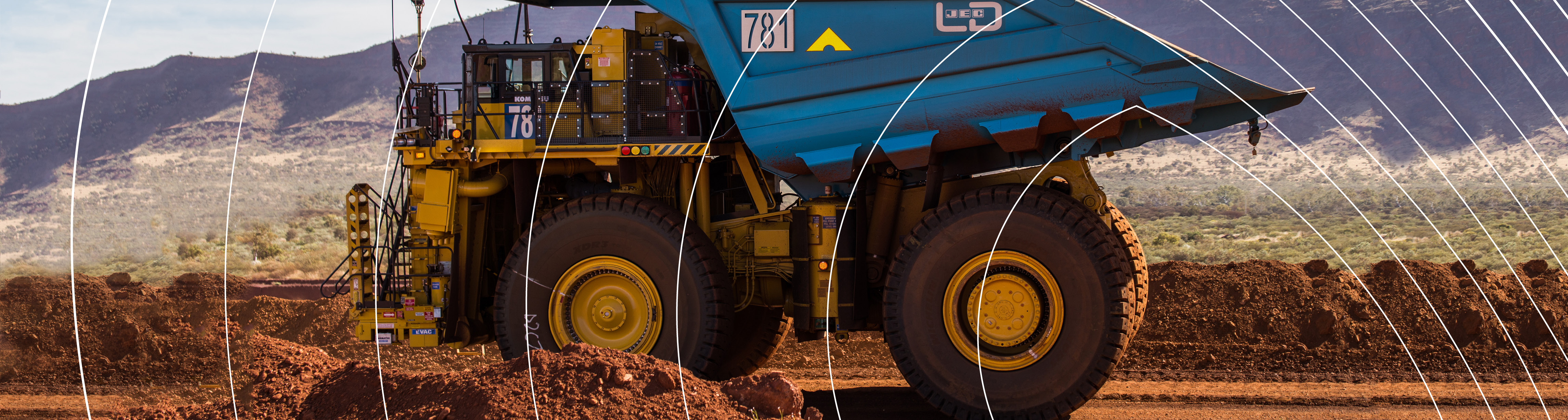
CASE STUDY: Rio Tinto Mining Automation
Case Studies
Since 2014, XM2 Aerial has been pioneering the use of unmanned aerial …
Go.Robot is an Australian company that distributes and configures robotic …
Laing O’Rourke – lifting frontline job satisfaction
Laing O’Rourke is a $AU6 billion international operation with 50 years of involvement …
Co-designing a robot for Indigenous Australian language revival
Opie the Robot is a technology deployed in classrooms in the southeast …
In the back streets of Brisbane, two brothers with a passion for the automative …
Share this story
Rio Tinto’s fleet of autonomous haul trucks have moved more than 1 billion tonnes of material to date. Since commencing trial operations in 2008, haul trucks fitted with autonomous haulage system (AHS) technology have now moved both ore and waste material across five sites in the Pilbara, including the newly commissioned Silvergrass mine. Last year, Rio Tinto’s autonomous fleet accounted for the movement of about a quarter of the total material moved across Pilbara mines. On average, each autonomous truck was estimated to have operated about 700 hours more than conventional haul trucks during 2017, with around 15 per cent lower load and haul unit costs. Importantly, there have been zero injuries attributed to autonomous haul trucks since deployment, highlighting their significant safety advantages [RT18].
Autonomous haulage systems used in mining are in high demand. The typical approach is to enhance existing mining trucks by integrating them with robust autonomous sub-systems. As an example, Komatsu introduced its FrontRunner® autonomous haulage system (codeveloped with Modular Mining Systems, USA) for use at Rio Tinto’s Pilbara iron ore operations in Western Australia. Meanwhile, at the Rio Tinto Pilbara mining site, about 100 autonomous trucks are operated. The trucks navigate the complex mining environment to deliver payloads of overburden and ore without drivers. This is revolutionising productivity and mine operations, especially at mines where it is difficult to secure sufficient labour, owing to their remote locations.
Trending Article
An Australian university (ANU) has been the first to trial intelligent drones for automated inspection of solar power plants.
The project is an industry-researcher collaboration funded by the Australian government’s Australian Renewable Energy Agency (ARENA) developing a cost-effective robotic inspection system…
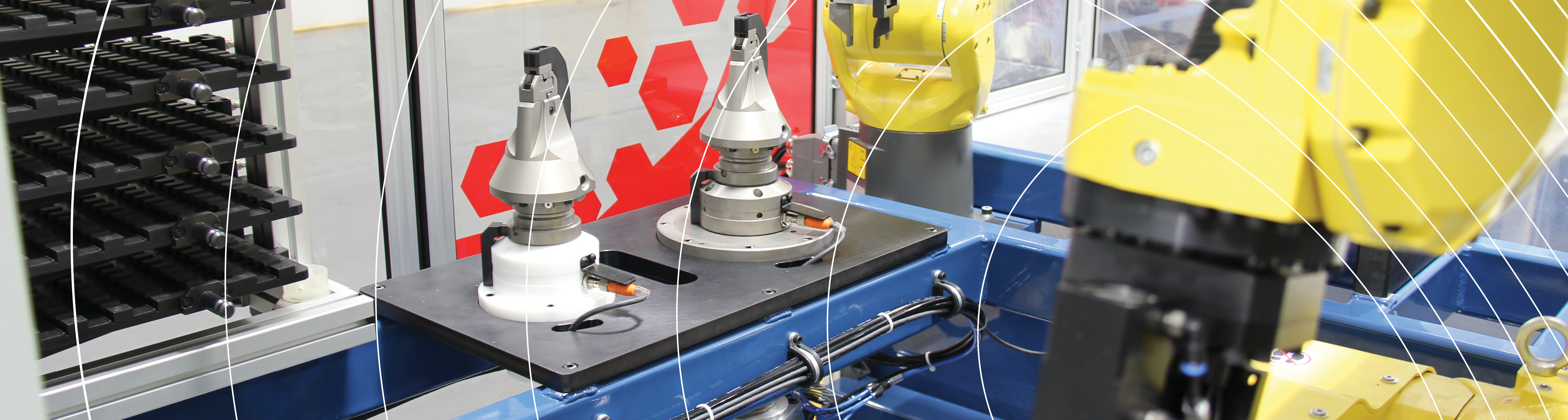
ANCA – Australia’s largest user of industrial robots
ANCA is an Australian company, founded in Melbourne in 1974, now with offices...
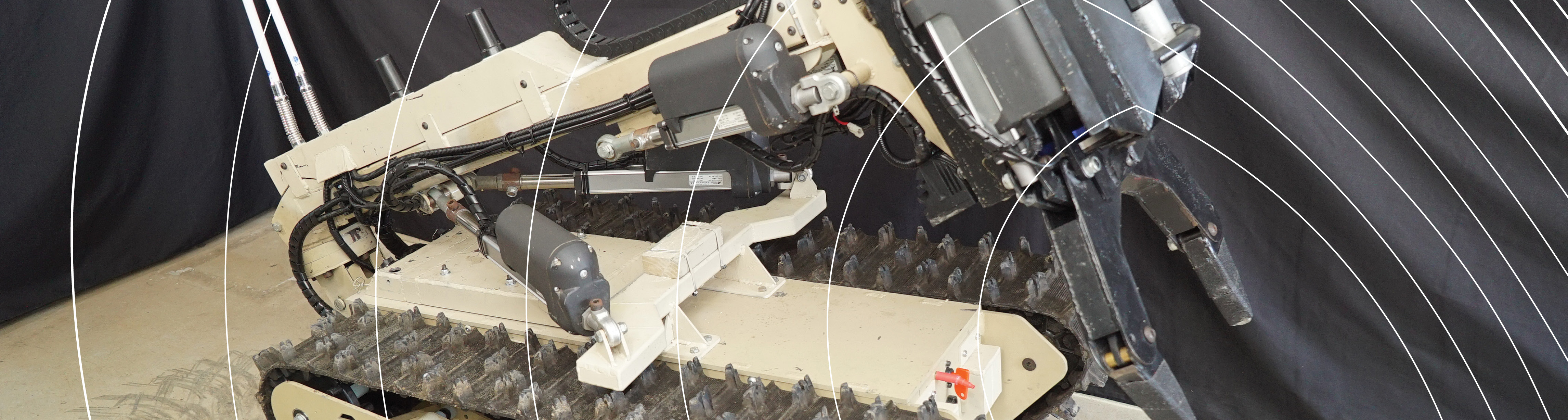
BIA5 Innovation Robotics and customers
BIA5 Pty Ltd is a start-up company that specialises in designing, manufacturing...
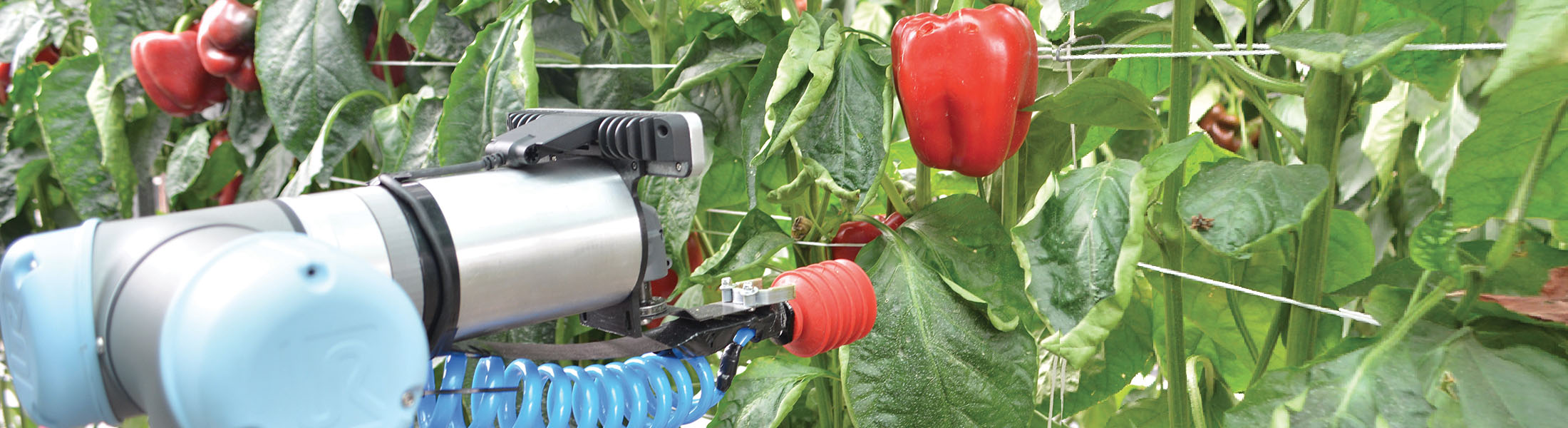
Harvey - the capsicum-picking robot
The horticulture industry in Australia has a gross value of more than $AU8...
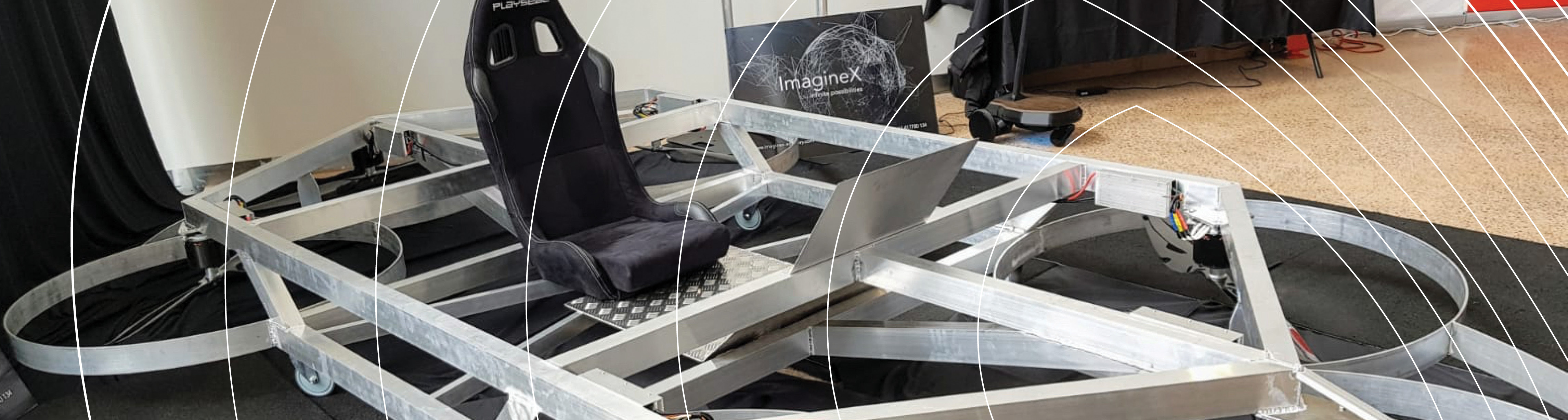
Pegasus Alpha – Flying car
In the back streets of Brisbane, two brothers with a passion for the automotive industry had a feeling that the future is vertical.